I have every easy out set under the sun but they never work well for me in most cases. The spiral socket type normally DOES work for me however these cap bolts on my w140 were so corroded no size would fit them.
One was snapped right off when I did try vice grips on it and heat from a torch.
So it was on to old trusty- my MIG welder. Never ever fails to get any stuck faster out. This is for 2 reasons:
Getting proper mechanical fastening onto any sheared or seized bolt head. You can weld a large nut on and be able to get more grip to apply torque VS say a small and rounded cap head.
Secondly it blasts red hot heat right down the old bolt / threads and this also breaks the rust / loctite bond.
Here is a good example:

Subject bolt:

Always first grind the head to clean metal. Otherwise the weld will be very porous and weak.

Find a big mild steel nut and hammer it on over the cap bolt head ready for the electric glue:


Then hit with some water to cool off and tap with a hammer to help loosen the threads bond. Spray some pentrating oil and start to work the bolt out.
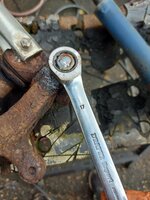
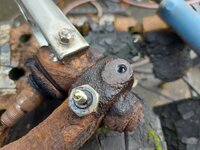
No damage to anything and this took only a couple minutes per bolt to do with all tools at hand.
Top Tip:
I find the welded nuts can sometimes twist off due to the high torque to remove really troublesome fasteners. To help with this a small impact on its lowest setting will work the bolt out really nicely:

And in this case I used a large old bolt to get great purchase and use the impact in a tight area. I used water to cool the weld quicky as I went and protect the ABS sensor.



This also works on sheared off bolts. Use a dremil to clean the end and carefully weld a washer and / or nut onto the remains:



Job done on this hub ready for de rusting and restoration:

Without the welder technique I would have spent hours with drills etc and probably ended up scrapping the part if anything went wrong. This is quick and 100% effective.
One was snapped right off when I did try vice grips on it and heat from a torch.
So it was on to old trusty- my MIG welder. Never ever fails to get any stuck faster out. This is for 2 reasons:
Getting proper mechanical fastening onto any sheared or seized bolt head. You can weld a large nut on and be able to get more grip to apply torque VS say a small and rounded cap head.
Secondly it blasts red hot heat right down the old bolt / threads and this also breaks the rust / loctite bond.
Here is a good example:

Subject bolt:

Always first grind the head to clean metal. Otherwise the weld will be very porous and weak.

Find a big mild steel nut and hammer it on over the cap bolt head ready for the electric glue:


Then hit with some water to cool off and tap with a hammer to help loosen the threads bond. Spray some pentrating oil and start to work the bolt out.
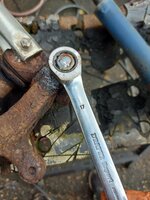
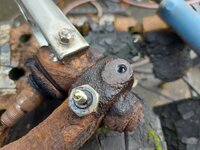
No damage to anything and this took only a couple minutes per bolt to do with all tools at hand.
Top Tip:
I find the welded nuts can sometimes twist off due to the high torque to remove really troublesome fasteners. To help with this a small impact on its lowest setting will work the bolt out really nicely:

And in this case I used a large old bolt to get great purchase and use the impact in a tight area. I used water to cool the weld quicky as I went and protect the ABS sensor.



This also works on sheared off bolts. Use a dremil to clean the end and carefully weld a washer and / or nut onto the remains:



Job done on this hub ready for de rusting and restoration:

Without the welder technique I would have spent hours with drills etc and probably ended up scrapping the part if anything went wrong. This is quick and 100% effective.