What with the current "self quarantine" imposed, I thought it a good time to begin a very long-standing project -- the complete refresh and cleaning of the top end of my M119 engine. Note that my E500 has 143K miles on it.
There was ZERO issue with running, other than the following small issues:
The caps and rotors had last been replaced around 2005, also when I lived in Portland. I did not notice any running issues due to the caps and rotors, since that time.
Over the past few years, I'd decided to do a complete refresh of the top end of the engine -- particularly all of the 'soft parts' -- because much of it was original, and now 26 years old.
Generally, the scope of the job is as follows:
So ... let's get started. My first night in the shop consisted of around 90 minutes of time, mainly taking apart the main top elements in the engine compartment, to expose other parts that will be the subject of actual repairs.
First off, here's an overview of the engine compartment. Typical M119 / W124 engine -- looks good, runs great. No complaints. Why am I embarking on this long journey, again !?!?!
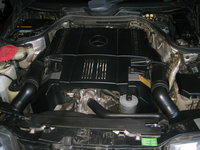
The first step, of course, is to DISCONNECT THE BATTERY in the trunk. Remove the positive or negative terminal from the battery, so that no power goes to the car's systems.
Next, you need to remove the plastic airbox and decorative cladding on the top of the engine. Remove the two "zoom tubes" that connect the air intakes to the airbox, and then remove the airbox as a unit. Set everything aside for safekeeping.

Next up, remove the two plastic covers that hide the caps and rotors. These should generally just pop off with a gentle flexing past the integrated clips.

From there, remove the two covers that hide the spark plug wires on each bank of the engine. A large flat-blade screwdriver (I used a "stubby") is excellent for getting a bite on the large plastic bolts that hold this cover to the top of the valve covers. Unscrew the bolts, and gently lift the cover off.

Then, do the same on the other side.
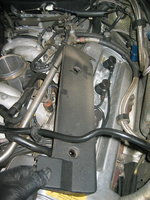
Upon removing the airbox and the covers for the spark plugs and wires, I came across the first red flag of the job -- a visually degraded throttle cable in the back part of the engine. Touching this throttle cable, pieces of the white adjusting screw flaked off, and you can also see literally broken pieces of plastic as part of the adjusting mechanism. So, add this to the list as the FIRST part that will require replacement. Fortunately, I believe I have one already in my parts stock (which I've had for probably 15 years there). And coincidentally, I just sent off a second spare cable YESTERDAY to one of our forum members.
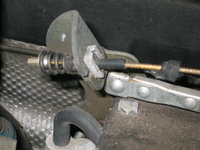
In the last photo above, you can also see the degradation in the whitened plastic grommet, just to the right of the spring in the photo. This is a $2.50 part from MB (and I believe also comes with a new throttle cable) -- and I believe that one of our members recently had this part fail, causing running issues. Since this part is so cheap, and important to the running of the vehicle, I recommend that you have a spare or two in your parts stock. I have FOUR spares, plus the one that is already installed on the throttle cable that I'll be replacing this one with.
So, with the plastic covers removed from the engine, here's what the "bare" M119 looks like, just before we start diving in to remove more parts.

It's time for the next stage, which is the removal of the distributor components -- namely the distributor caps, rotors, brackets and insulators. We'll remove and then carefully inspect their condition in a few minutes. Let's dive into exposing them for removal, for now.
Using a pair of special "spark plug" pliers, grasp each ignition connector at the cap, twist it slightly (1/8 of a turn should break it loose), and pull it straight off of the terminal on the distributor cap. You can do this with your fingers, but having a pair of special pliers to do this makes the job about 80% easier (and easier for installation, eventually, too). Remove all four of the connectors for the cylinders on each cap, plus the central coil wire connector.

You may want to use a "Sharpie" or other pen and label each distributor cap's terminal as to the plug wire cylinder number that it corresponds to. I did this for the passenger side, and then didn't bother to do it for the driver's side, because of THIS......

Yes, that is what you think it is -- a CRACKED distributor cap ! Another part for the "replacement" list -- although cap/rotor/insulator replacement was going to be included in this job anyway.
So, the next step is to remove the distributor caps. You need a 5mm Allen socket or Allen key to do this. DO NOT use the "ball" end of an Allen key for cap or rotor removal -- ONLY a straight end that is not beveled. This will ensure that the bolts do not get stripped out. The next few photos show the removal of the caps, using a couple of different tools. A 5mm "swivel" Allen socket comes in handy for the bottom bolts on the caps, which are difficult to reach. These are the SAME 5mm swivel sockets that are used for removal of the back bolts on the valve covers, so are a worthwhile investment.
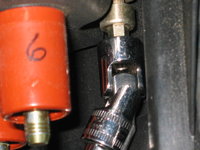
After the three bolts on each cap are removed, pull the cap off and inspect it. Here's what I found on the inside of my passenger-side cap (remember, these had been last replaced around 2006, so nearly 14 years ago!):

Not horrible, but not that great eather. You can see a couple of carbon tracks between the center (coil) piece and two of the contacts. This would result in some misfiring or other minor hiccups in running, though to be honest I never really saw or felt any running problems. BUT, the caps could stand for replacement. Still, not bad for ~14 years old.
Here is a view of things with the cap removed:

Earlier, I forgot to remove two plastic pieces, so did it now -- the two plastic air intake pieces that comprise the back-side of the headlights, which the zoom tubes connect to. These lift straight up and out. Keep these pieces safe, as they are both NLA from MB.

More inspection of the cap from the driver's side. Note that it is aftermarket Bosch, October 2005 production date. Not as bad as the passenger side -- not much in the way of arc traces.
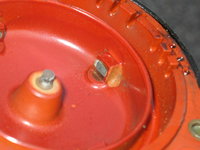
Now it's time to remove the rotors, and the brackets they attach to. The rotors attach via three 3mm bolts, and the brackets attach via a single, 5mm central bolt. It is IMPERATIVE again that you NOT use beveled or rounded Allen keys to remove the rotor and bracket bolts. ONLY use straight-edged Allen keys and Allen sockets to avoid stripping out these bolts.

After careful removal and inspection of the rotors, it's time to remove the 5mm bolt holding the rotor bracket on.

After the bracket comes off, the insulators will come right off of the cylinder head. Time to inspect them carefully. These were the original, blackBosch Doduco insulators that my car came with. You can see that they do not have a lot of wetness or condensation on them, thankfully. The orange rubber seal on the front side is very smashed and flattened down.

After removal of the insulators, you can see the actual end of the cylinder heads. A couple of observations here: 1) some oil leakage is observed on both sides. This tells me that there is a modest (not severe) oil leak at the cam seals, which will necessitate replacing both sides' cam seals. This shouldn't be too big of a deal, but yet another part to place on the order list.

Next up, it's time to remove the plastic pieces that are bolted to the ends of the cylinder heads, that surround the distributor caps. These are extremely thin pieces of plastic, and can get quite brittle. I found that, while mine came off OK, on one side, two tabs cracked off, and on the other side, one small crack developed. These are cheap parts (around $15 apiece, discounted, from MB), and so I will place them on my parts order list -- although I will keep the "old" ones as they are in good enough condition.
Each of these plastic pieces is held on by three 5mm Allen bolts. Two of the bolts on each side are difficult to get at, and are best reached with a long Allen key, or your 5mm "swivel" socket using a 1/4" drive and an extension. The bottom-most bolts, you have to pretty much remove by "feel".
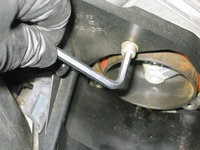
It had been a few years since my tandem pump refirbishment and the replacement of the "short hose" between the reservoir and tandem pump, so it seemed like an opportune time to see how the short hose was holding up. You can see here a couple of views of the short hose with the four clamps I'd placed on it. Some modest seeping of fluid, but no outright leaks. I will clean up the area and snug down each of the clamps, but otherwise things seemed more or less OK. It actually looks a bit worse in the photos than it did to my naked eye. A couple of shots of brake cleaner will make short work of this area, when the timne comes....

Here is a shot of the vacuum wire routing in the area near the tandem pump. You can see the corrugated wire conduit, most of which has flaked off and disappeared. I will be replacing all of this conduit at the time of reassembly, with new conduit that is hopefully heat resistant. This should clean things up and restore a more factory appearance to things.

The next phase of the job entails removing all of the connectors on the intake manifold that pertain to the upper wiring harness. I'd had my harness replaced back around 2005, so I was in good shape with it, and a visual inspection of the end connectors confirmed that it is holding up very well. The next photos are of the removal of various connectors at sensors on the cylinder head and intake manifold. Several connectors cracked from heat, so new parts to replace them will be ordered. They are very inexpensive to replace.


Next up was removal of the EGR valve, which sits atop the intake manifold. This is held on by three 5mm Allen bolts, and there is a gasket underneath the valve that will require replacement upon reassembly. There is a vacuum connection in the area -- both to the EGR valve itself, and to a nipple atop the intake manifold. The following photos show the removal of these vacuum connectors, and of the EGR valve itself.

The next thing to do is to remove all eight spark plug wires, plus the two coil wires, from the engine compartment. This will make more room for the future steps.

Next up, you need to begin removing the rubber air intake hoses from their fittings on the valve covers. Just lift them up -- you'll remove the actual hose assembly in a few minutes.

Here's what the engine looks like with the plug wires removed.

In the process of removing the vacuum connectors from the EGR valve and nearby nipple on the intake, one of the vacuum lines literally pulled out in my hand. It had already cracked (and you can see a short, newer section of vacuum line from a repair I'd done when I lived in Texas). This is very likely the cause of the "EGR inoperative" failure that I'd been reciving CHECK ENGINE lights for, over the past few years. The vacuum line was completely cracked off between the EGR valve and the smog pump area where it led to. So this will need, obviously, to be replaced with new vacuum line.

Here is the removal of various bolts that hold the plastic frame for the upper wiring harness to the top of the intake manifold. These are 5mm and 6mm Allen bolts, and are quite easily despatched. At this point, you should also unclip each of the eight fuel injector connectors by squeezing the metal wires together at each injector, and pulling the connector straight off of the injector.

Here you can see the thick plastic connector for the upper wiring harness to the MAF. Twist the MAF wire connector and work it up and out of the way.

At this point, with all of the upper wiring harness connectors removed, you can lift the upper harness out of the way and fold back over the CAN box area.
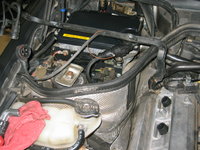
Next up, you need to disconnect the vacuum line that goes from the intake manifold to the brake booster. This is a semi-flexible plastic line, and it may or may not still be good. Use a 17mm open-end wrench, along with a 19mm wrench, together to loosen the connector. Unscrew the connector and do your best to move the vacuum line out of the way.

Next up, you will need to begin disassembly and removal of the fuel rail. It is held onto the top of the intake manifold by a bunch of 10mm bolts Here I remove a couple of them, but will continue the process in the next part of this HOW-TO.

Next up is the removal of the intake air rubber hose system from the top of the intake manifold. Here you can see me clipping a zip tie that had been placed between one of the hoses and the fuel rail, to keep them together. This had been done when the nitrous-oxide system had been installed on my car in the 2004-2005 time frame. I will replace this zip tie upon reassembly, but for now it is one of the last hurdles to removing the intake air hoses. Note the gummy dirt on the outside of the hoses in the third photo below -- likely because of the vapor from the intake that traveled through them, attracting dirt and detritus.

Finally, removal of the complete air hose system from the top of the engine. All of my hoses, which were all quite still flexible, were in good condition. I have replacements for all of them, and will probably use them on the rebuild.

And lastly, foreshadowing the next phase of the job ... the MAF and its ring clamp bolt.

Stay tuned for the next installment of this HOW-TO, where I'll be showing the removal of the fuel rail and fuel injectors, removal of the MAF, and then removal of the intake manifold "stack" itself.
Thanks for watching, so far.
There was ZERO issue with running, other than the following small issues:
- a small but annoying engine oil leak from the valve cover, resulting in oil dropping onto the exhaust manifold and smelling
- a persistent set of two codes being thrown over the past few years -- an EGR code and an "air injection inop" code, resulting in a CHECK ENGINE light being lit (and recurring after being cleared)
- A leaking front crankshaft seal, resulting in a small but persistent few drops of oil on the floor after every drive of the car.
The caps and rotors had last been replaced around 2005, also when I lived in Portland. I did not notice any running issues due to the caps and rotors, since that time.
Over the past few years, I'd decided to do a complete refresh of the top end of the engine -- particularly all of the 'soft parts' -- because much of it was original, and now 26 years old.
Generally, the scope of the job is as follows:
- Replace all vacuum lines in the upper engine area
- Replace rubber intake air tubes (if needed)
- Replace suspected lazy thermostat with new Wahler unit
- Proactively rebuild original ETA wiring
- Replace soft parts at intake manifold -- fuel injector seals, intake manifold gaskets and seals, etc.
- Replace upper timing chain rails
- Clean out likely clogged EGR tube inside intake manifold
- Separate and have halves of intake manifold hot-tanked
- Replace transmission cooling hoses
- Replace heater hoses at back of engine
- Replace smog pump hoses
- Replace front crankshaft seal
- Replace two ignition coils
- Replace ceramic resistor
- Inspect distributor caps, rotors, and insulators and replace if needed
- Inspect other plastic and soft parts and replace if needed
- Replace cracked/broken/missing plastic conduit in engine compartment
- Replace cam covers with red covers I had powder-coated two years ago
- Replace very crunchy hood pad with new hood pad
- Change transmission fluid, filter and pan gasket
- Perform any other maintenance and repair underhood as needed
So ... let's get started. My first night in the shop consisted of around 90 minutes of time, mainly taking apart the main top elements in the engine compartment, to expose other parts that will be the subject of actual repairs.
First off, here's an overview of the engine compartment. Typical M119 / W124 engine -- looks good, runs great. No complaints. Why am I embarking on this long journey, again !?!?!
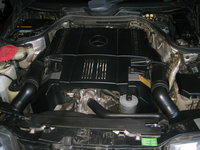
The first step, of course, is to DISCONNECT THE BATTERY in the trunk. Remove the positive or negative terminal from the battery, so that no power goes to the car's systems.
Next, you need to remove the plastic airbox and decorative cladding on the top of the engine. Remove the two "zoom tubes" that connect the air intakes to the airbox, and then remove the airbox as a unit. Set everything aside for safekeeping.




Next up, remove the two plastic covers that hide the caps and rotors. These should generally just pop off with a gentle flexing past the integrated clips.




From there, remove the two covers that hide the spark plug wires on each bank of the engine. A large flat-blade screwdriver (I used a "stubby") is excellent for getting a bite on the large plastic bolts that hold this cover to the top of the valve covers. Unscrew the bolts, and gently lift the cover off.


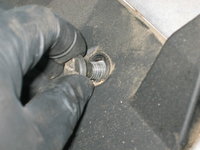

Then, do the same on the other side.

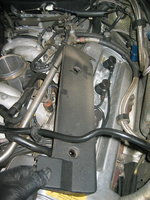
Upon removing the airbox and the covers for the spark plugs and wires, I came across the first red flag of the job -- a visually degraded throttle cable in the back part of the engine. Touching this throttle cable, pieces of the white adjusting screw flaked off, and you can also see literally broken pieces of plastic as part of the adjusting mechanism. So, add this to the list as the FIRST part that will require replacement. Fortunately, I believe I have one already in my parts stock (which I've had for probably 15 years there). And coincidentally, I just sent off a second spare cable YESTERDAY to one of our forum members.

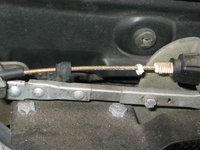
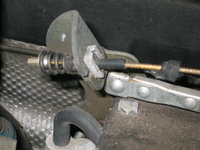
In the last photo above, you can also see the degradation in the whitened plastic grommet, just to the right of the spring in the photo. This is a $2.50 part from MB (and I believe also comes with a new throttle cable) -- and I believe that one of our members recently had this part fail, causing running issues. Since this part is so cheap, and important to the running of the vehicle, I recommend that you have a spare or two in your parts stock. I have FOUR spares, plus the one that is already installed on the throttle cable that I'll be replacing this one with.
So, with the plastic covers removed from the engine, here's what the "bare" M119 looks like, just before we start diving in to remove more parts.

It's time for the next stage, which is the removal of the distributor components -- namely the distributor caps, rotors, brackets and insulators. We'll remove and then carefully inspect their condition in a few minutes. Let's dive into exposing them for removal, for now.
Using a pair of special "spark plug" pliers, grasp each ignition connector at the cap, twist it slightly (1/8 of a turn should break it loose), and pull it straight off of the terminal on the distributor cap. You can do this with your fingers, but having a pair of special pliers to do this makes the job about 80% easier (and easier for installation, eventually, too). Remove all four of the connectors for the cylinders on each cap, plus the central coil wire connector.




You may want to use a "Sharpie" or other pen and label each distributor cap's terminal as to the plug wire cylinder number that it corresponds to. I did this for the passenger side, and then didn't bother to do it for the driver's side, because of THIS......

Yes, that is what you think it is -- a CRACKED distributor cap ! Another part for the "replacement" list -- although cap/rotor/insulator replacement was going to be included in this job anyway.
So, the next step is to remove the distributor caps. You need a 5mm Allen socket or Allen key to do this. DO NOT use the "ball" end of an Allen key for cap or rotor removal -- ONLY a straight end that is not beveled. This will ensure that the bolts do not get stripped out. The next few photos show the removal of the caps, using a couple of different tools. A 5mm "swivel" Allen socket comes in handy for the bottom bolts on the caps, which are difficult to reach. These are the SAME 5mm swivel sockets that are used for removal of the back bolts on the valve covers, so are a worthwhile investment.


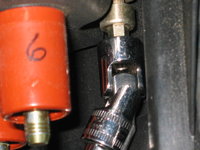
After the three bolts on each cap are removed, pull the cap off and inspect it. Here's what I found on the inside of my passenger-side cap (remember, these had been last replaced around 2006, so nearly 14 years ago!):



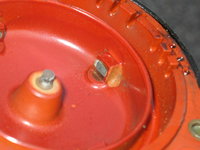

Not horrible, but not that great eather. You can see a couple of carbon tracks between the center (coil) piece and two of the contacts. This would result in some misfiring or other minor hiccups in running, though to be honest I never really saw or felt any running problems. BUT, the caps could stand for replacement. Still, not bad for ~14 years old.
Here is a view of things with the cap removed:

Earlier, I forgot to remove two plastic pieces, so did it now -- the two plastic air intake pieces that comprise the back-side of the headlights, which the zoom tubes connect to. These lift straight up and out. Keep these pieces safe, as they are both NLA from MB.

More inspection of the cap from the driver's side. Note that it is aftermarket Bosch, October 2005 production date. Not as bad as the passenger side -- not much in the way of arc traces.


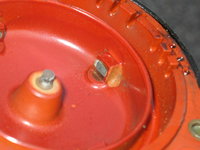
Now it's time to remove the rotors, and the brackets they attach to. The rotors attach via three 3mm bolts, and the brackets attach via a single, 5mm central bolt. It is IMPERATIVE again that you NOT use beveled or rounded Allen keys to remove the rotor and bracket bolts. ONLY use straight-edged Allen keys and Allen sockets to avoid stripping out these bolts.




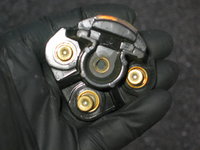

After careful removal and inspection of the rotors, it's time to remove the 5mm bolt holding the rotor bracket on.
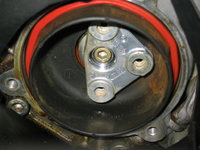
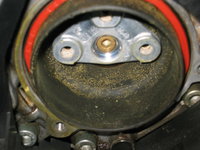
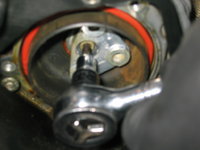

After the bracket comes off, the insulators will come right off of the cylinder head. Time to inspect them carefully. These were the original, black




After removal of the insulators, you can see the actual end of the cylinder heads. A couple of observations here: 1) some oil leakage is observed on both sides. This tells me that there is a modest (not severe) oil leak at the cam seals, which will necessitate replacing both sides' cam seals. This shouldn't be too big of a deal, but yet another part to place on the order list.
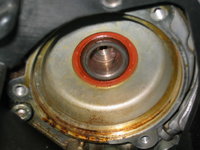



Next up, it's time to remove the plastic pieces that are bolted to the ends of the cylinder heads, that surround the distributor caps. These are extremely thin pieces of plastic, and can get quite brittle. I found that, while mine came off OK, on one side, two tabs cracked off, and on the other side, one small crack developed. These are cheap parts (around $15 apiece, discounted, from MB), and so I will place them on my parts order list -- although I will keep the "old" ones as they are in good enough condition.
Each of these plastic pieces is held on by three 5mm Allen bolts. Two of the bolts on each side are difficult to get at, and are best reached with a long Allen key, or your 5mm "swivel" socket using a 1/4" drive and an extension. The bottom-most bolts, you have to pretty much remove by "feel".
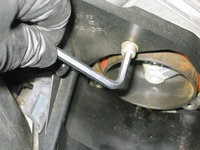
It had been a few years since my tandem pump refirbishment and the replacement of the "short hose" between the reservoir and tandem pump, so it seemed like an opportune time to see how the short hose was holding up. You can see here a couple of views of the short hose with the four clamps I'd placed on it. Some modest seeping of fluid, but no outright leaks. I will clean up the area and snug down each of the clamps, but otherwise things seemed more or less OK. It actually looks a bit worse in the photos than it did to my naked eye. A couple of shots of brake cleaner will make short work of this area, when the timne comes....
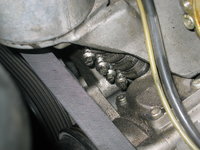

Here is a shot of the vacuum wire routing in the area near the tandem pump. You can see the corrugated wire conduit, most of which has flaked off and disappeared. I will be replacing all of this conduit at the time of reassembly, with new conduit that is hopefully heat resistant. This should clean things up and restore a more factory appearance to things.

The next phase of the job entails removing all of the connectors on the intake manifold that pertain to the upper wiring harness. I'd had my harness replaced back around 2005, so I was in good shape with it, and a visual inspection of the end connectors confirmed that it is holding up very well. The next photos are of the removal of various connectors at sensors on the cylinder head and intake manifold. Several connectors cracked from heat, so new parts to replace them will be ordered. They are very inexpensive to replace.
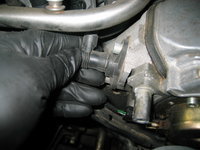
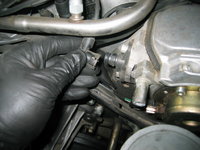



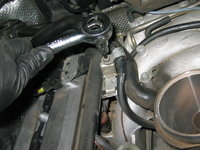

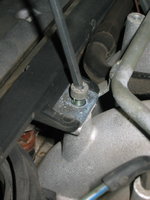
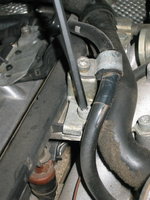

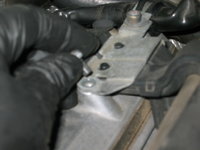


Next up was removal of the EGR valve, which sits atop the intake manifold. This is held on by three 5mm Allen bolts, and there is a gasket underneath the valve that will require replacement upon reassembly. There is a vacuum connection in the area -- both to the EGR valve itself, and to a nipple atop the intake manifold. The following photos show the removal of these vacuum connectors, and of the EGR valve itself.




The next thing to do is to remove all eight spark plug wires, plus the two coil wires, from the engine compartment. This will make more room for the future steps.

Next up, you need to begin removing the rubber air intake hoses from their fittings on the valve covers. Just lift them up -- you'll remove the actual hose assembly in a few minutes.

Here's what the engine looks like with the plug wires removed.

In the process of removing the vacuum connectors from the EGR valve and nearby nipple on the intake, one of the vacuum lines literally pulled out in my hand. It had already cracked (and you can see a short, newer section of vacuum line from a repair I'd done when I lived in Texas). This is very likely the cause of the "EGR inoperative" failure that I'd been reciving CHECK ENGINE lights for, over the past few years. The vacuum line was completely cracked off between the EGR valve and the smog pump area where it led to. So this will need, obviously, to be replaced with new vacuum line.

Here is the removal of various bolts that hold the plastic frame for the upper wiring harness to the top of the intake manifold. These are 5mm and 6mm Allen bolts, and are quite easily despatched. At this point, you should also unclip each of the eight fuel injector connectors by squeezing the metal wires together at each injector, and pulling the connector straight off of the injector.



Here you can see the thick plastic connector for the upper wiring harness to the MAF. Twist the MAF wire connector and work it up and out of the way.


At this point, with all of the upper wiring harness connectors removed, you can lift the upper harness out of the way and fold back over the CAN box area.
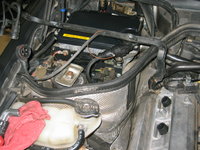
Next up, you need to disconnect the vacuum line that goes from the intake manifold to the brake booster. This is a semi-flexible plastic line, and it may or may not still be good. Use a 17mm open-end wrench, along with a 19mm wrench, together to loosen the connector. Unscrew the connector and do your best to move the vacuum line out of the way.
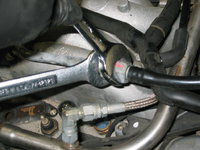

Next up, you will need to begin disassembly and removal of the fuel rail. It is held onto the top of the intake manifold by a bunch of 10mm bolts Here I remove a couple of them, but will continue the process in the next part of this HOW-TO.


Next up is the removal of the intake air rubber hose system from the top of the intake manifold. Here you can see me clipping a zip tie that had been placed between one of the hoses and the fuel rail, to keep them together. This had been done when the nitrous-oxide system had been installed on my car in the 2004-2005 time frame. I will replace this zip tie upon reassembly, but for now it is one of the last hurdles to removing the intake air hoses. Note the gummy dirt on the outside of the hoses in the third photo below -- likely because of the vapor from the intake that traveled through them, attracting dirt and detritus.



Finally, removal of the complete air hose system from the top of the engine. All of my hoses, which were all quite still flexible, were in good condition. I have replacements for all of them, and will probably use them on the rebuild.

And lastly, foreshadowing the next phase of the job ... the MAF and its ring clamp bolt.

Stay tuned for the next installment of this HOW-TO, where I'll be showing the removal of the fuel rail and fuel injectors, removal of the MAF, and then removal of the intake manifold "stack" itself.
Thanks for watching, so far.