About three or four hours in the shop over the past couple of days, as I am definitely starting to see light at the end of the tunnel.
First, I took a look at my handiwork after completing the headlight install, along with the washer reservoir, and the associated vacuum plumbing to the switchover valves in the area. It was very satisfying to see that everything had been done and refurbished in this area. I actually removed the washer fluid reservoir again, and replaced the small rubber foot that held the forward end of it into the small bracket. It was a small thing, but seeing I had vowed to replace everything rubber in the engine compartment..... and it came in a very timely manner in my latest parts order (took only two days to get it).
After that, it was time to break out my shop air compressor to take care of a couple of clean-up jobs — mainly blowing out the intake valve areas on each cylinder, and also to blow out the spark plug holes for replacement of the spark plugs. I had not replaced the spark plugs since early 2009, not long after I moved to Texas.
So, I broke out my skinny nozzle for the end of my air compressor's hose, and attached it. Then I went to work blowing out each cylinder's intake valves. Blowing them out REALLY made a big difference and got a lot more stuff out than I had done (or could do) manually, despite spending a couple of hours trying to do so. I did one pair of valves at a time, and then covered them back up so that no additional removed dirt and crud got back into them.
Then I blew out each spark plug hole.
Broke out a brand-new box of vintage Bosch (made in Gemany) MB F8DC4 plugs from my parts stash.
And using my special swivel "GearWrech" 3/8" magnetic socket adapter, obtained a while back from Amazon, I replaced each spark plug. Torque for each plug is 28 Nm. I did NOT put any anti-seize paste on the threads of each plug.
And broke out the new, fresh plugs. Gap for each new plug is
1.0mm, or (English system) 0.0395 inch (I used
0.040 inch as indicated on the gapper).
And....installing each plug, one by one.
Next, it was time to turn my attention installing the intake manifold to the cylinder heads. Before I did this, I laid out all of the intake manifold bolts, as shown below. There are three lengths of bolts -- two LONG ones, four medium ones, and eight shorter ones. And a bracket, which goes onto one of the medium bolts.
As a rule of thumb, the bolt pattern is as follows:
- The two long bolts go in the front-most, inner positions on the intake manifold.
- The four medium bolts go in the four rear-most (inner and outer) bolts closest to the firewall. The medium bolt with the bracket goes in the inside rear position on the driver's side (I'll show this later in a photograph).
- The eight short bolts go in along the inside sides of the intake manifold.
Before test-fitting the manifold into place, I needed to do a few steps first. First, I removed all of the duct-tape that I had used to cover the intake and coolant ports. It's important to remove any left-over adhesive junk from the tape on the gasket sealing surface. I cleaned the gasket sealing surface by lightly wiping it with a towel soaked in brake cleaner. This served as a "final clean" before test-fitting the manifold in place. I then also did a visual check to make sure everything was out of the way at the back of the engine (accelerator linkage, and so forth.
The first photo below shows what things looked like before I removed the new Elring intake manifold gaskets from their packaging, and put them into place. Note that each gasket has two small holes that fit two pins on each side that are in the surface of the cylinder head. The fourth photo below shows one of these pins. The pins help keep the gasket in place as you are lowering the intake manifold down into place.
Gaskets in place, and ready to accept the test-fit for the intake manifold assembly.
Intake manifold, all cleaned and ready for test-fitment.
And .... lowering into place and test fitting the manifold.
Test fitment was successful, so I removed the manifold and went to take care of one more thing — the installation of the vacuum line that runs from the lower inside of the manifold out the front to the EZL, and also the larger vacuum line that runs from the "MOT" fuel vapor valve near the EZL, through the front of the intake manifold area and up through the middle of it to the rubber air lines (which will be installed later). The length of the small plastic vacuum line (in white below) that goes directly to the EZL is 1.4 meters; the length of the larger black vacuum line to the MOT valve is 1.6 meters.
Both of these lines came from the factory with the corrugated plastic covering, which flakes apart with heat cycles and age, so after I cut the requisite lengths of tubing, I also cut an appropiate length of the black flexible heat-resistant sheathing to cover the lines as they exited the manifold area and routed up to the EZL area. Of course, I used new rubber connectors, as specified in the ISPPI. In the fourth photo below, you can see the larger black "MOT" vacuum line sticking straight upward through the intake runners, just to the right of the MAF.
Next, in preparation for the final fitment of the intake manifold, I broke out the new length of coolant hose that connects the intake manifold to the top of the water pump housing. The third photo below shows the new and old lengths of hose side by side. As I lowered the intake manifold into position, I removed the lint-free cloth I'd inserted a some time ago to keep dust out of the water pump, and fitted the hose and its two clamps into place.
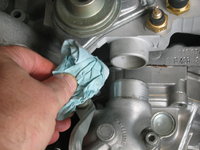
With some wriggling, I got the hose fitted into place, and used my screwdriver to tighten the two clamps. DON'T over-tighten the clamps, but do make sure they are snug.
This is the intake manifold dropped into place, ready to accept all of the bolts.
Next, now that the intake manifold assembly was fitted into place, it was time to bolt it down with all 14 of the intake manifold bolts. As I loosely dropped each bolt down into place, I applied a SMALL dab of anti-seize paste into the threads of each one. Just a dab, though.
After each bolt was dropped into its slot (but not yet tightened), I did the final routing and adjustment for the two aforementioned vacuum lines, and routed them out of the manifold and over to the driver's side of the engine for final installation in the near future.
Here is what things look like, with all 14 of the bolts loosely installed, and the vacuum lines routed appropriately. The second photo shows the tightening down of all of the 14 bolts to their specified 28 Nm (~20 lb-ft) torque with my medium-range torque wrench.
As mentioned before, here is the placement of the metal bracket on the inner-most rear "medium" length intake manifold bolt.
I did not yet tighten down the last two "longest" intake manifold bolts -- these are done last and have some things that attach to them before they are tightened down. But, with the intake manifold basically now in place, I connect the two vacuum lines that I'd previously replaced that go to the EGR valve, and to the nipple on the top of the manifold. Again, new rubber connectors. These are the two lines that come from the switchoever valves on the inside of the passenger-side fender, behind the headlight, and are routed through the top of the smog pump bracket.
And, that is all for now. Again, as I go along, I'm constantly cleaning, detailing and vacuuming out things to make them clean again.
More soon, and thanks for your interest !!